The European company Innofil3D is a well known producer of high quality filament. We had the chance to talk to Roger Sijlbing about their newest products and more.
Just last month Innofil3D presented their all new PRO1 filament. The first of a new product line for professionals. Innofil3D has gained lots of know how in the 3D printing space since the company was founded in 2012 as a subsidiary of Applied Polymer Innovations (API). The knowledge in the material space comes from the parent company. But a lot was going on in the last four years.
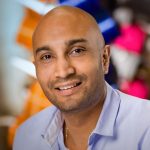
How did you first make contact with additive technologies or 3D printing?
Roger Sijlbing: Innofil3D was introduced to 3D printing back in 2012. Applied Polymer Innovations (API) our parent company was approached by a 3D-printer manufacturer who was buying it’s filaments in USA. They were not satisfied with the quality and logistically it was easier to buy filaments in Europe. API has over 25 years of experience in the development, analysis and shaping of polymer fibres. API has its own pilot plant facility for development purposes. As an expert in analysing polymer (filament) behaviour we developed a process to produce high quality filaments which was easily scalable.
In which industries do you see the most potential for filaments and materials from Innofil3D? Did additive technology already entered industries you wouldn’t have thought of?
I see a 3D-printing as a tool. A tool which has the biggest potential for companies that create products: the manufacturing industry. Developing a new product or even improving existing products is very costly and 3D-printing can offer a cost effective and time-saving alternative to other methods. In the prototyping phase 3D-printing is a great asset to manufacturing companies because it is fast and cheap. Within the industries you see verticals which clearly benefit from the 3D-printing tool such as:
- Automotive – the creation of tools for assembly and prototypes
- Aviation – the creation of tools for service and prototypes
- Machine building – prototyping parts and assessing the impact on maintenance
- Construction – assessing if models will fit in certain profiles or structures
- Architecture – creating Marquette
There is one customer who really surprised me and that was a cookie company. Beside baking cookies they also gave workshops and at the end of each workshop the participants wanted the cookie cutters. So the company (who didn’t have any design skills) decided to print the cookie cutters which they sold at their workshop. Because of the success they now also sell online.
For future developments I believe it is time for the next level. To offer manufacturing companies more than a prototyping tool we need to develop materials which have engineering capabilities for functional use. Innofil3D is currently in a phase in which we are assessing how to incorporate properties like for example strength, high temperature resistance, conductivity, stiffness, impact resistance etc. in filaments for FDM printing. This requires a solution oriented approach to material development and also collaboration with manufacturers of raw materials and 3D-printer manufacturers. We could do this with existing material grades or we could develop special compounds. Our newly release PRO1 is an example of a special compound. We created a solution which offers increased productivity through higher operating speeds, high strength and easy to use. We first assessed the properties and then develop a material that fits these requirements. For the industry it is also important to have access to actual data and figures such as the strength of printed parts. We have this data available for all our standard materials and PRO1.
It is clear that 3D-printing has many advantages to offer to the industry but it is our responsibility to develop materials which offer added value. This is crucial for the evolution of our own industry.
How would you describe the connections in the 3D Printing ecosystem (hardware, software, materials,…)? Your company provides one of these parts – materials. How do they work together? How crucial are hardware and software for successfully using Innofil3D filament?
The triangle software, hardware and materials are very much connected because it influences the end-result. For example: when a user decides to invest in a 3D-printer you want the first experience to blow them away. You don’t want them to be disappointed because they use poor quality materials. Poor software will generate models that will never achieve the full potential of the printer or material. It is mystery to me why people would invest in high quality machine but fail to use high quality filaments or software. Because the relationship is so crucial users should be more conscious off the effects. In the end a 3D-printer is a precision machine and as we all know: garbage in is garbage out!
With the launch of the new PRO1 filament Innofil3D created a new line of materials for professionals. As I wrote the PRO1 combines the printability of PLA and the material properties of ABS. And it is very affordable too. Have I forgotten any of the features? Are there any downsides you can think of?
The most important features are increased productivity due to a higher operation speeds and high performance because of its strength. We have seen strength as an important development in the 3D-printing industry. Professional users want to print stronger objects so it can be used for functional purposes. The closer the output of the 3D-printer gets to the mass production methods the more beneficial it will be and the more applications it will serve.
As we all know that time is money for business. By increasing the operation speeds 3D-printing will become a more viable alternative to other production methods thus more appealing to the professional users. We have proof that PRO1 prints at least 3x faster than existing materials without reducing the quality of the print. With conventional settings you achieve stronger printed objects. We can back this up with data from tests which are conducted according to international standards. To successfully launch the Professional Series we wanted the first product not only to have engineering properties but also easy to use. This again reduces printing time and print failures. That is one of the key benefits of PRO1.
What are the next steps for Innofil3D? Will we see more developments in the professional line or will you surprise us with completely new materials?
We have chosen the strategy to develop filaments for professional use because we believe that we have the organization, knowledge and experience to fulfil the demands of this target group. Our background is applied polymer research. Our facility offers us tools to not only develop high end materials but to also provide data regarding material behaviour. We are the first to have done extensive research on 3D-printed specimens according to ISO regulations and added features (like printing in the Z-directions) to the test method to take variables into account. PRO1 is the first solution driven product release and there will be more to come from Innofil3D in this segment.
If you are interested in more news about Innofil3D you can find them here in our news section or on the homepage of Innofil3D.
You also can find more 5Questions-interviews of other industry experts.
Subscribe to our Newsletter
3DPresso is a weekly newsletter that links to the most exciting global stories from the 3D printing and additive manufacturing industry.